Chat&Coffee with…Vincenzo Provenzano
Berti resumes the column Chat&Coffee, to go in search of a young talent in the world of design who, like us, sees parquet as one of the protagonists in interior design choices. He is Vincenzo Provenzano who has been working in Jeddah since 2010 as Chief Architect for the UDG (Urban Design Group) studio. After initial training at local technical firms, he specialized in sustainability issues and eco-friendly architecture. He has been in Jeddah (KSA) since 2010. We met with him to chat and get an insider’s perspective on a market as interesting and always a source of new developments and projects as Saudi Arabia.
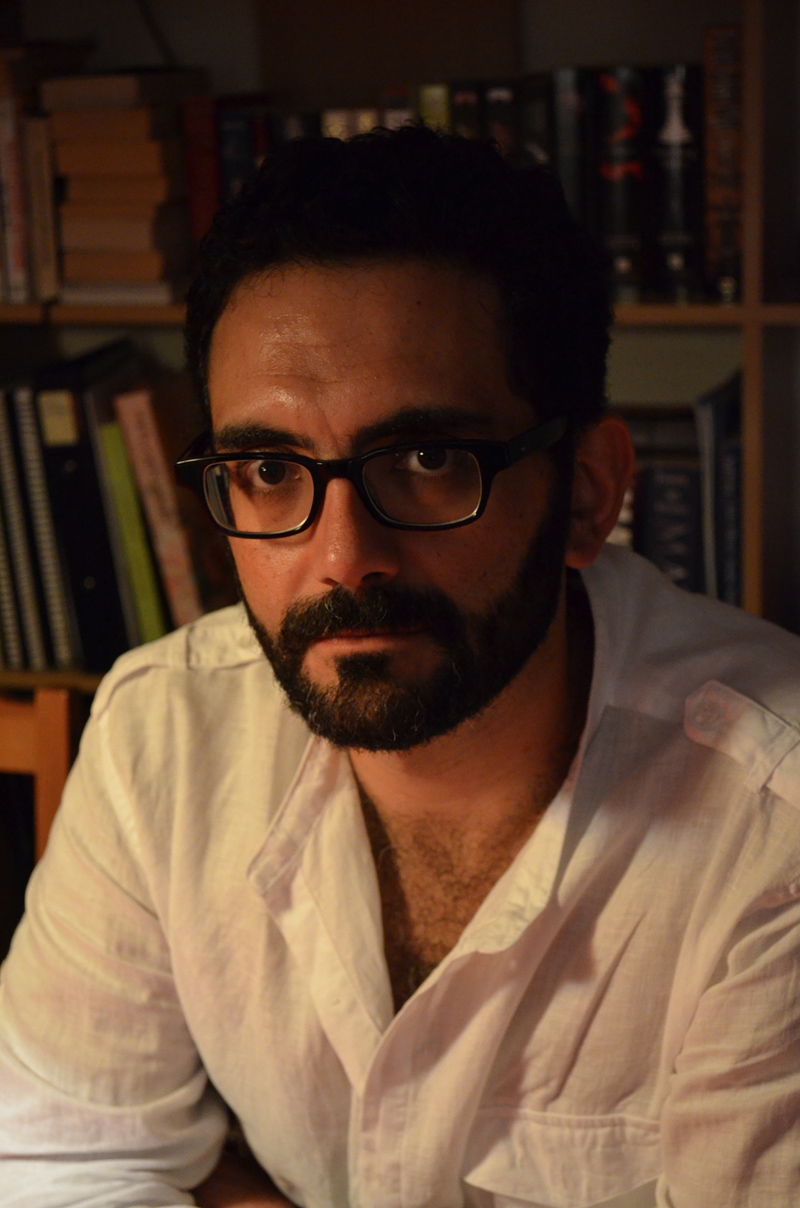
What are the motivations for a young Italian architect to move abroad?
I could trivially say that in a time of crisis like the one we are experiencing, the main motivation for us to go abroad is to simply find a job.
In reality, the problem is much more complex than it seems, as architects of recent generations in Italy have generally found several obstacles to entering the workforce, both in the private sector and in local government.
Regarding the private sector specifically, in my opinion in recent years in Italy there has been a gradual decrease in the ‘authority of the figure of the architect. This must be combined with the consideration of the impressive decline suffered by the construction sector, which has also happened in Europe.
But in the end what drives us most of all to make a sharp turn in our lives, often tired of the difficulties we find in our homeland, is the desire to work in a more dynamic reality than Italy: in my case I have the opportunity to pursue projects in a country that is constantly expanding and with a significant economic availability like Saudi Arabia. The same thing happens, on the other hand, in many other fields. Many young professionals and researchers, who in Italy do not have the opportunity to establish themselves, in fact go abroad where they manage to emerge because they are encouraged by more favorable situations.
How do you find working in Saudi Arabia? What are the challenges and opportunities this market presents?
I would say that I can consider myself quite lucky: I have the opportunity to work as Chief Architect in a young, professional and growing reality. UDG (Urban Design Group) was born, in fact, as an interior design studio, but it is gradually establishing itself in the field of architecture as well: my challenge is precisely to conquer more and more space in this sector by proposing quality design that detaches itself and emerges from the local design reality, which often remains stuck on concepts that are no longer so current. Of course, here I often have the opportunity to take care of quite important projects: not only in terms of size, which is far beyond our standards, but also in terms of the quality of the materials used and custom-made elements.
How important is it and how is Made in Italy received abroad?
Here in Saudi Arabia and in the Middle East in general, Made in Italy enjoys great prestige: the customer knows that if he wants quality materials, in terms of finishes or furnishings, he surely must turn to the Italian market, which is unquestionably synonymous with luxury.
Italian designers also enjoy a certain authority: this is thanks not only to the esteem in which our country is held around here and around the world, but also to the education we have received in our universities, which we too often despise.
Tell us about a particular project of yours?
The project I have been working on lately, and which is now nearing completion, is a complex of four waterfront homes in a recently expanded area north of Jeddah.
It originated as an extension of a Balinese-style resort overlooking the Red Sea and newly built: the client’s request was for the expansion of the resort with the creation of a separate section of four villas for their children.
Since the available lot is narrow and long, with the short side facing the sea, the main problem that arose was to provide all dwellings with a sea view.
My proposal aimed to solve this problem, together with the desire to propose in a contemporary key a Balinese architecture not only in form, but especially in substance. I started, therefore, from those morphological elements that determine the specificity of Balinese buildings, without necessarily dwelling on the decorative elements typical of their places of origin.
The four dwellings were thus integrated into a single complex (based on a module of 1.20×1.20 meters) articulated in different volumes arranged in a U-shape around a central courtyard, open only in the direction of the sea. The basic elements are represented by different platforms placed on different levels sloping toward the sea, made of Bianco Inici marble, alternating with different water mirrors, garden parts, and a swimming pool integrated into a porch on the first floor.
The whole has been conceived as a set of alternating masses and voids, trying to maintain as much continuity’ as possible between interior and exterior space: the masses are represented by stone parallelepipeds without openings in which the bathrooms and other services are located; the voids, on the other hand, consist of large sliding glass windows with Iroko frames and suitably treated for the purpose of filtering the sun’s rays.
The materials chosen were essentially three: stone, marble and wood. Freshly polished stone was used for facade cladding and some interior rooms. Marble (size 60×120 cm and 120×120 cm, with a satin steel finish) was used for most of the interior and exterior floors. Wood, on the other hand, for some interior and exterior facades and bedroom floors. The parquet used is a mocha oak, made by Berti specifically for this project: in fact, I needed a dark wood that had the same shade as the exposed fixtures and beams, but at the same time resistant to moisture to be used also in the bathrooms, in many cases open to the respective bedrooms. Berti was the best answer for this need. It is a Heat-baked oak, which has undergone a sophisticated process with the aim of increasing the cohesion and compactness of the fibers, while providing excellent mechanical and strength properties. The heat-treatment process gives the wood a uniform, darker color: by adjusting the time and temperature, it was possible to achieve the shade suitable for the environment.
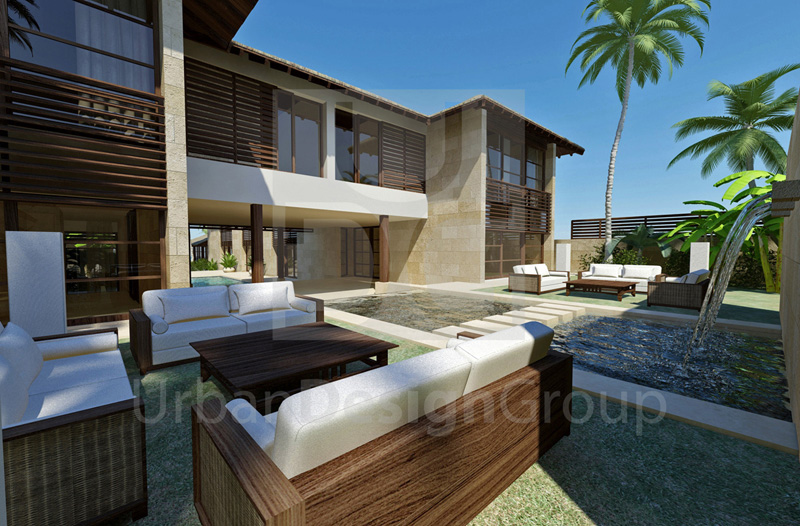
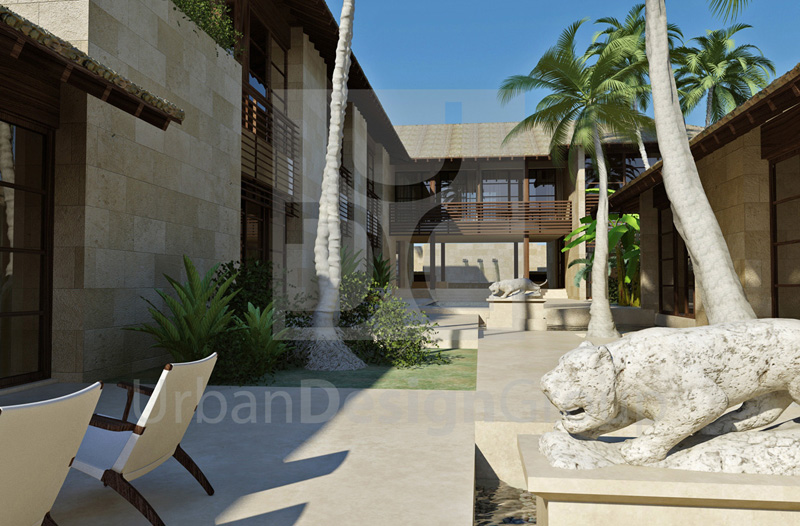
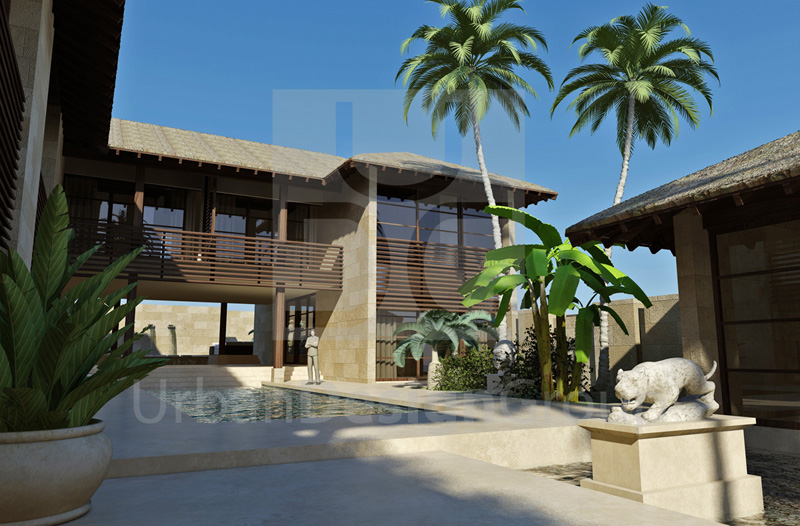
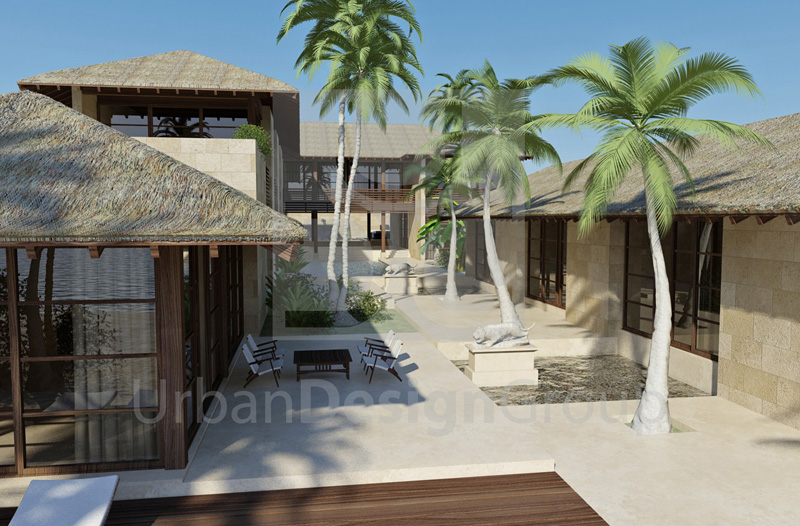
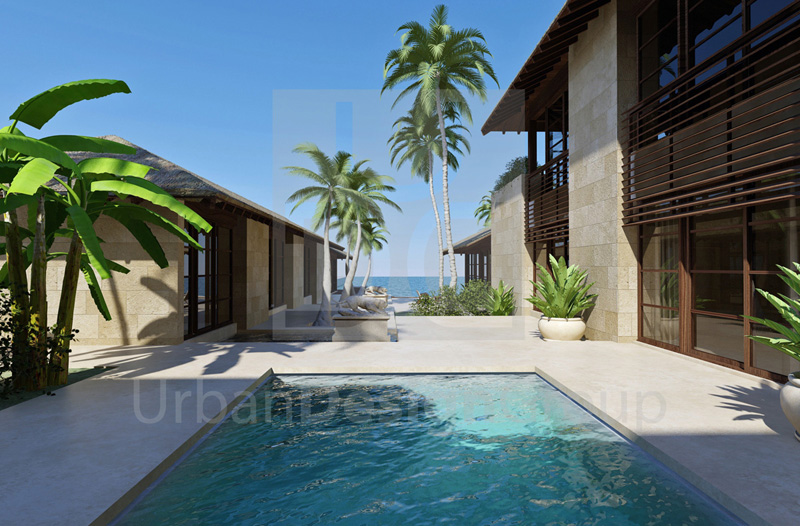